Also known as air flow visualisation, the goal is to demonstrate visual evidence of air flow direction. Airflow patterns minimise contamination in a controlled environment. Smoke visualisation of air patterns is a direct way of assessing a cleanroom design and the suitability of HVAC AC system in relation to HEPA filtered air diffusion. The results highlight the efficacy of air contamination control and could be required by a regulatory body such as the MHRA.
Proper airflow prevents contamination and should be an integral part of your cleanroom design. It diagnoses problems that mitigate operations in a cleanroom such as excess contamination in an area.
Saakvee Technologies is a leader in the design and installation of mission-critical ventilation systems as well as testing and maintenance. Our professional engineers are adept at carrying out smoke testing and identifying accurate airflow and problems that need rectifying.
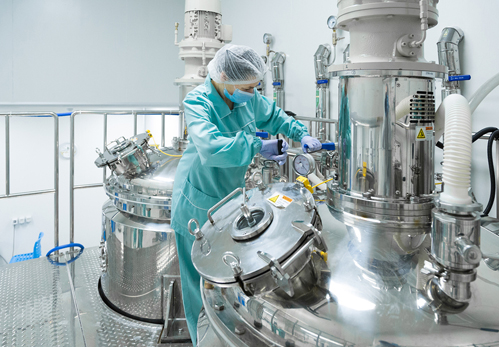
Saakvee Technologies carries out smoke testing in your controlled environment or cleanroom with a pharmaceutical grade smoke chemical consisting of pure water and Glycerine BP grade. They aim to
- Locate faults in areas of excessive contamination buildup in one area
- Check design and performance specs of a controlled space or environment
- Monitor the effect of operator interventions on unidirectional airflow into controlled environment enclosures.
Humans and machinery are the major sources of contamination in a cleanroom. Airflow patterns could be easily disturbed with equipment design, machine guarding, necessary interventions and inappropriate component specifications.
Through a smoke test, it is easy to see where an airborne contaminant will likely end up using visual evidence of air flow direction.
Modular Cleanroom Benefits
- Modular Construction
- Quick Assembly Time
- Versatility
- Reconfiguration
- Airflow Control
- Inexpensive Modifications
Desired Airflow Characteristics In A Cleanroom
Air should flow smoothly in one direction without eddies or turbulence. Air disruption should quickly recover to regain unidirectional flow for movement within the air stream.
Airflow should move away from the product path and towards potential sources of contamination. That is, HEPA filtered air should not flow over the product path after flowing over cleanroom personnel.
Cleanroom Design, Build & Validation
- Budgeting and planning
- Engineering, design & layout
- Airflow and filtration design
- Construction and Installation
- Full Certification of our product
- Industry-specific equipment installation
- Validation
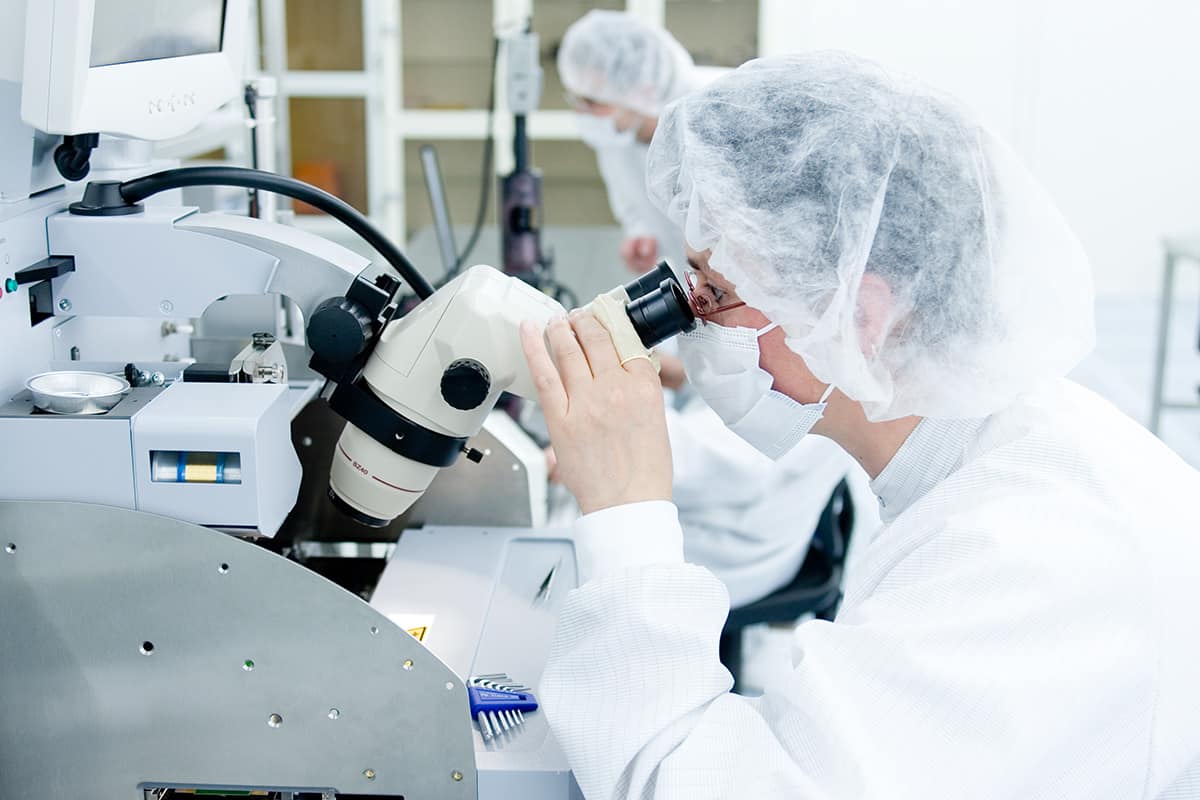
Saakvee Technologies Smoke Testing Services
Smoke studies are used to maintain aseptic conditions when sterile products are manufactured under aseptic conditions. Smoke studies demonstrate sweeping action and unidirectional airflow over and away from the product, and the testing is conducted under both dynamic and static conditions.
Smoke testing should be well planned. It should include the evaluation of the impact of equipment design and aseptic manipulations such as interventions. Recorded videotapes serve as objective evidence that shows that the cleanroom is a proper manufacturing environment to external regulators and internal auditors.
Modular Cleanroom Services
- Design & Build
- Free Site Survey
- Free Design Service
- Cleanroom Planning
- Construction and Installation
- CNC Engineered
- Training & Support
- Discounted Service Contracts
- Remedial Works
- Panel Repairs
- Alternations
- BMS Management
- Cleanroom Certification
- Differential Pressure Qualification
- Servicing Testing Validation
- Smoke Testing
- DOP Testing
At Saakvee Technologies we carry out smoke testing and critical airflow visualisation studies. Our experience extends to planning, consulting and execution of smoke testing projects.
We provide services such as project management, protocol development and execution, data analysis, digital recording and summarisation of interventions. Other services include
- dynamic and static airflow visualisation studies of biological safety cabinets, cleanrooms, isolators, clean benches and related clean air devices to ensure they comply with regulatory bodies and international aseptic guidelines
- smoke testing to evaluate BSC placement and performance
- evaluating the impact of alternative BSC usage scenarios through bespoke containment testing of bio-safety cabinets.
- thoroughly documented test results with quality Smoke testing also includes a DVD recording.
At Saakvee Technologies, our services are offered by certified staff. We also offer customised report documentation made to fit your needs and management of your service records and equipment inventory.
Cleanroom Features
- GMP
- ISO 4-9
- ISO 14644
- Low Power Consumption
- Environmentally Friendly
- HEPA Filters
- Air Filtration
- Fan Filter Units
- Cleanroom Ceiling System
- Temperature Control
- Access Control
- Inter Lock Door Systems
- Air Showers
- Unidirectional Airflow
- Desiccator Cabinets
- Horizontal Flow Wall Modules
- Horizontal Laminar Flow Clean Benches
- Laminar flow cabinets
- Laminar Flow Canopy
Performing A Clean Zone Smoke Test
When using a uni-directional flow device in a compounding process, the customers, suppliers and certifiers should be familiar with the following terms
DCS: Direct compounding area is a critical area with the ISO class 5 where critical sites are knowingly exposed to first air.
First air: Air coming out from the HEPA filter in a particle-free unidirectional air stream.
Critical site: A location that includes openings, touch contamination, components and fluid pathway surfaces such as injection ports, vial septa and beakers. The exposure time and the size of the openings increase the risk of microbial particulate contamination.
To test a clean zone, there are several issues such as dead spots, smoke deviations and smoke reflux to look for. The HEPA filter media should be flush with the front shield and walls of the clean zone. In its area of opening, the lexan shield should remain consistent in its area of opening from the HEPA filter through the travel of the ISO-5 zone. The type of filter utilised could affect airflow velocity uniformity, such as a room side replaceable ULPA or HEPA filter.
When selecting the filters for the clean zones, special consideration is given to filter manufacturers to ensure uniformity of face velocities among filter types. Unidirectional flow or uniformity is important to the functionality of these systems and a continuous low-level return.
Cleanroom Industries/Sectors
The purpose of the smoke pattern test is to determine that airflow within the clean zone is in line with the manufacturers’ design. It shows airflow moving with no refluxing or dead spots in a downward direction within the critical site. At Saakvee Technologies, we ensure that ambient air only enters through the HEPA filter.
Acceptable smoke sources include glycol-base smoke generators or chemical smoke tubes that are neutrally buoyant. The best results are achieved through a theatrical fog generator using a mixture of glycol and fan speed controller hooked to a delivery tube and supported by a hands-free stand.
After carrying out the procedure, we will discuss the reading with you if it exceeds a 14-degree offset. Corrections or approvals will be made until it is acceptable. The test will be performed as “at-rest”, “as-built” and “operational phase”. Other tests that should be performed include HEPA filter leak test, airflow velocity, airflow volume and uniformity test.